Sustainable Solutions for EV Battery Recycling: An Advanced Optimization Framework
Researchers from MIT propose a two-stage stochastic optimization model for EV battery recycling, demonstrating significant cost reductions and environmental benefits through strategic investment and advanced optimization techniques. This model enhances recycling efficiency, addressing critical supply chain challenges for lithium-ion batteries.
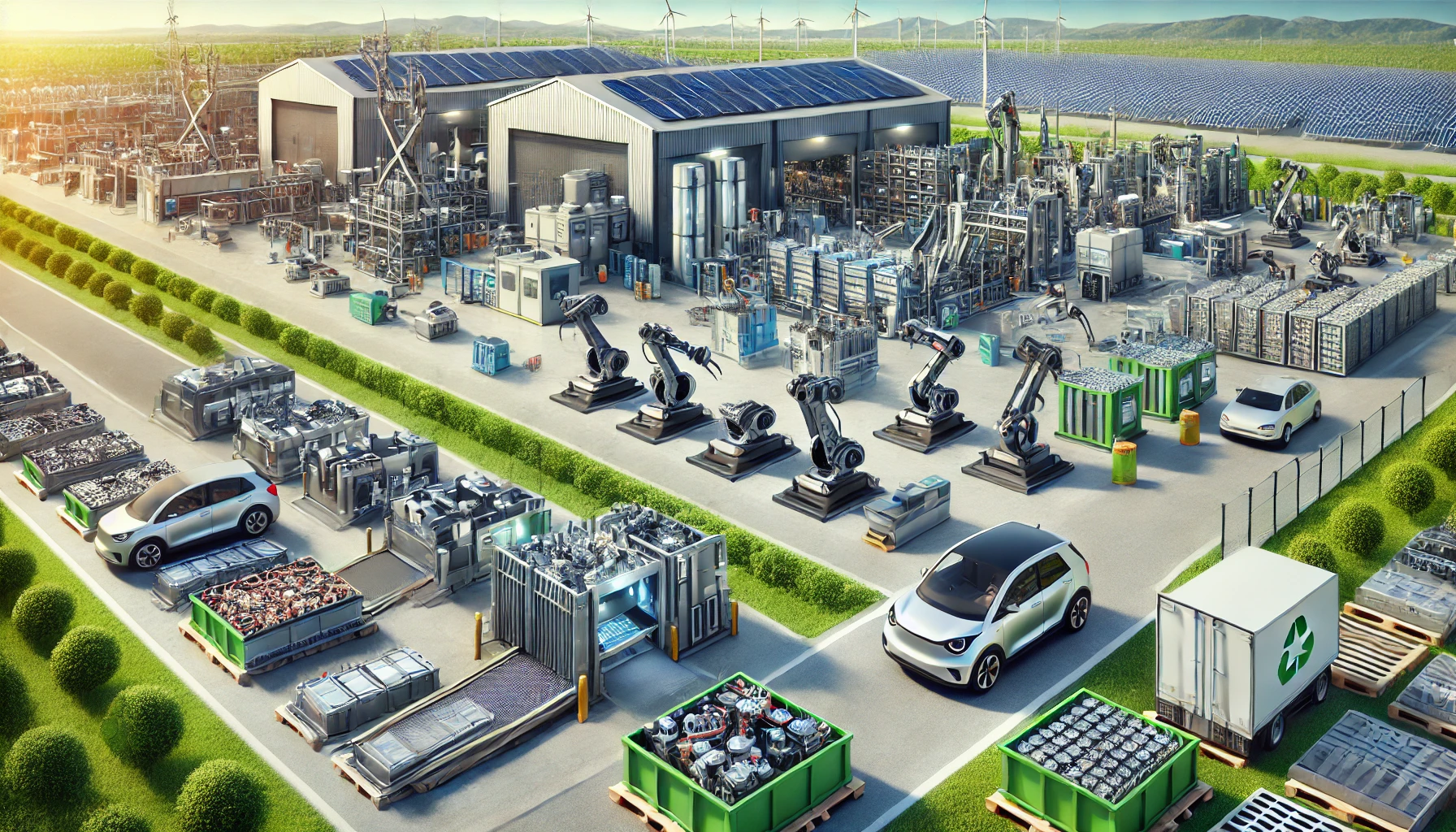
The electric vehicle (EV) battery supply chain faces significant challenges related to sourcing scarce, expensive minerals required for battery manufacturing and disposing of hazardous retired batteries. Integrating recycling technology into the supply chain can mitigate these issues, but it necessitates strategic investment planning for recycling facilities. Researchers from the Massachusetts Institute of Technology (MIT) propose a two-stage stochastic optimization model for minimizing the cost of recycling capacity decisions, wherein retired batteries are recycled and recovered materials are reused in new battery production. The model employs a separable concave minimization approach with linear constraints and introduces a new global optimization algorithm based on piecewise linear approximation, which solves problems up to ten times faster than existing algorithms. Additionally, a reformulation of the model reduces the number of variables by integrating integrality constraints, leading to significant reductions in solve times. The study also explores a cut grouping strategy for Benders’ decomposition in the second stage, enhancing convergence compared to traditional methods.
Meeting the Rising Demand for Lithium-Ion Batteries
The rapid growth in demand for lithium-ion batteries, driven by the energy transition and the increasing adoption of EVs, underscores the urgency of addressing these challenges. The manufacture of these batteries relies heavily on critical minerals like lithium, cobalt, nickel, and manganese, which are prone to supply chain disruptions. As demand for these materials surges, efficient recycling becomes imperative. Retired batteries, which typically have a lifespan of around ten years, must be safely disposed of to avoid environmental and health hazards. The European Union has already implemented regulations requiring recycled materials in new batteries and setting targets for material recovery from retired batteries. Recycling offers a promising solution by recovering valuable materials from retired batteries for reuse. Technologies such as pyrometallurgical, hydrometallurgical, and direct recycling processes are employed for this purpose. Pyrometallurgical recycling involves high-temperature processes to recover compounds from cathode materials, while hydrometallurgical recycling uses chemical reactions to precipitate compounds. Direct recycling, a newer approach, employs mechanical processes to separate materials, followed by chemical treatments to restore them.
Innovative Recycling Technologies to Boost Sustainability
The EverBatt model, a recently proposed closed-loop framework, analyzes the cost and environmental impacts of battery recycling and manufacturing. In this model, recycled materials are used in new product manufacturing, differing from open-loop models where recovered materials are sold or disposed of. The study adapts the EverBatt framework into a two-stage stochastic concave minimization model. The first stage involves multi-year capacity decisions for recycling and cathode production facilities, followed by second-stage operational decisions based on scenarios of new battery demand, retired battery supply, and material costs. The study's contributions include the development of a novel adaptive piecewise linear approximation algorithm (aPWL) for the problem class, which demonstrates significant performance improvements over benchmark algorithms. The reformulation of the model to reduce the total number of variables further enhances solve times. The application of a Benders’ decomposition approach to the second-stage scenarios, with an innovative cut grouping strategy, yields faster convergence.
Substantial Cost Savings and Environmental Benefits
The computational analysis of the optimal solutions highlights the substantial benefits of effective recycling investment. Optimal recycling investment can reduce battery manufacturing costs by 22% and decrease environmental impacts by up to 7%. The study provides a comprehensive approach to addressing the critical challenges in the EV battery supply chain through strategic facility planning and advanced optimization techniques. A deeper dive into the problem reveals that EV batteries have variable lifespans but are generally retired after a capacity reduction of 20%, with an expected age of around ten years. The study recognizes the importance of safe disposal, as EV batteries contain toxic and heavy metals that pose health and environmental risks if improperly disposed of. Recent European Union regulations have set recycled material composition requirements for new batteries and material recovery targets from retired batteries. The proposed recycling technologies aim to recover valuable metals contained in battery cathode compounds, with pyrometallurgical recycling exposing battery packs to high temperatures to induce chemical reactions, hydrometallurgical recycling reacting cathode materials with a leaching solution to precipitate compounds, and direct recycling using mechanical processes to separate materials followed by chemical treatments to restore them.
Transforming the EV Battery Supply Chain
The EverBatt model is a closed-loop model that uses recycled materials for manufacturing new products, differing from open-loop models where recovered materials are sold or disposed of. The study adapts the EverBatt framework into a two-stage stochastic concave minimization model, with multi-year capacity decisions for recycling and cathode production facilities in the first stage, followed by second-stage operational decisions based on scenarios of new battery demand, retired battery supply, and material costs. The contributions of this study include the development of the adaptive piecewise linear approximation algorithm (aPWL) for the problem class, demonstrating significant performance improvements over benchmark algorithms. The reformulation of the model to reduce the total number of variables further enhances solve times. The application of a Benders’ decomposition approach to the second-stage scenarios, with an innovative cut grouping strategy, yields faster convergence. In conclusion, the computational analysis of optimal solutions highlights the substantial benefits of effective recycling investment. Optimal recycling investment can reduce battery manufacturing costs by 22% and decrease environmental impacts by up to 7%. This comprehensive approach to addressing the critical challenges in the EV battery supply chain through strategic facility planning and advanced optimization techniques showcases the potential of integrating recycling technology into the EV battery supply chain.
- FIRST PUBLISHED IN:
- Devdiscourse
ALSO READ
India's Electric Vehicle Surge: A Path to 28 Million EVs by 2030
Rheinmetall Revs Up for Defense Boom Amid Political Shifts
UPDATE 1-Tesla signs deal for first India showroom to sell imported EVs
European Union leaders back new spending plans aimed at freeing up billions for Europe's security, reports AP.